In this article, you’ll see just how much technology and expertise go into the manufacture of thermal transfer ribbons Click through to discover the details!
What may look like a simple printing ribbon is actually packed with advanced technology. These essential products, used for printing labels in various industries, go through a complex manufacturing process to ensure high quality, durability, and cost savings. Made with wax, resin, or a combination of both, they work with specialized inks to deliver excellent print quality and long-lasting results.
In this article, you’ll discover how this process works, along with other key details and the essential materials that give these ribbons their unique properties. Read on!
What are thermal transfer ribbons and how are they made?
Also known as TTR, thermal transfer ribbons are the key components used in thermal transfer printing. Essentially, they are a type of plastic film coated on one side with ink and on the other with silicone—this silicone layer is crucial to the process, as it helps dissipate heat during printing.
When the product passes through the printer head and is heated, the ink is released and transferred onto the material, typically a label, creating the printed image. This means that the ribbon plays a vital role in ensuring high-quality prints.
Depending on the type used, the coating may include wax, resin, or a combination of both. Each type offers different benefits, with wax providing high-quality prints for short-term use, and resin offering superior durability for long-lasting prints. Thermal transfer ribbons are essential for achieving precise, legible, and durable labels in various industries.
What are the different layers of a thermal transfer ribbon?
This is a simplified explanation, as these ribbons rely on other essential elements in their manufacture, such as those described below:
- Backcoat: A specialized technology designed to extend the life of the printhead by applying a protective layer of silicone. Positioned on the back of the ribbon, it remains in contact with the printhead, safeguarding it from friction with the labels during the printing process.
- Release Layer: This crucial layer sits between the polyethylene terephthalate (PET) and the ink. It ensures proper adhesion of the film during the thermal transfer printing process, allowing for a successful transfer of the ink onto the labels.
- Polyester Film (Carrier): A thin film that forms the backbone of the ribbon, providing a structure that holds the chemical layers in place. Its primary function is to maintain the integrity of the printed image during the thermal transfer printing process, ensuring the durability of the labels.
- Ink: The ink layer is transferred to the labels during the printing process. Formulated with pigment, it can contain wax, resin, or a combination of both, depending on the desired durability and print quality.
- Trailer: Positioned at the end of the thermal transfer ribbon, the trailer is a film that ensures the printer halts when the ribbon is nearing its end, preventing damage to the printer.
- Core: Made of cardboard or plastic, the core is the central shaft around which the ribbon is wound and unwound during the printing process, providing the structure needed for smooth operation.
- Leader: A PET layer that protects the ribbon, identifies its formulation, and makes it easy to change in the printer, ensuring a seamless transition between ribbons during printing tasks.
What is a thermal transfer ribbon used for?
A thermal transfer ribbon is used primarily in thermal transfer printing, where it plays a crucial role in transferring ink onto materials such as labels, tags, and packaging. The ribbon is heated by the printer’s printhead, causing the ink to melt and transfer onto the surface of the material, creating a durable print. Thermal transfer ribbons are commonly used for printing barcodes, text, and graphics on labels that need to withstand harsh environments, such as exposure to heat, moisture, chemicals, and abrasion. They are widely used in industries such as manufacturing, logistics, healthcare, and retail for labeling products and inventory management.
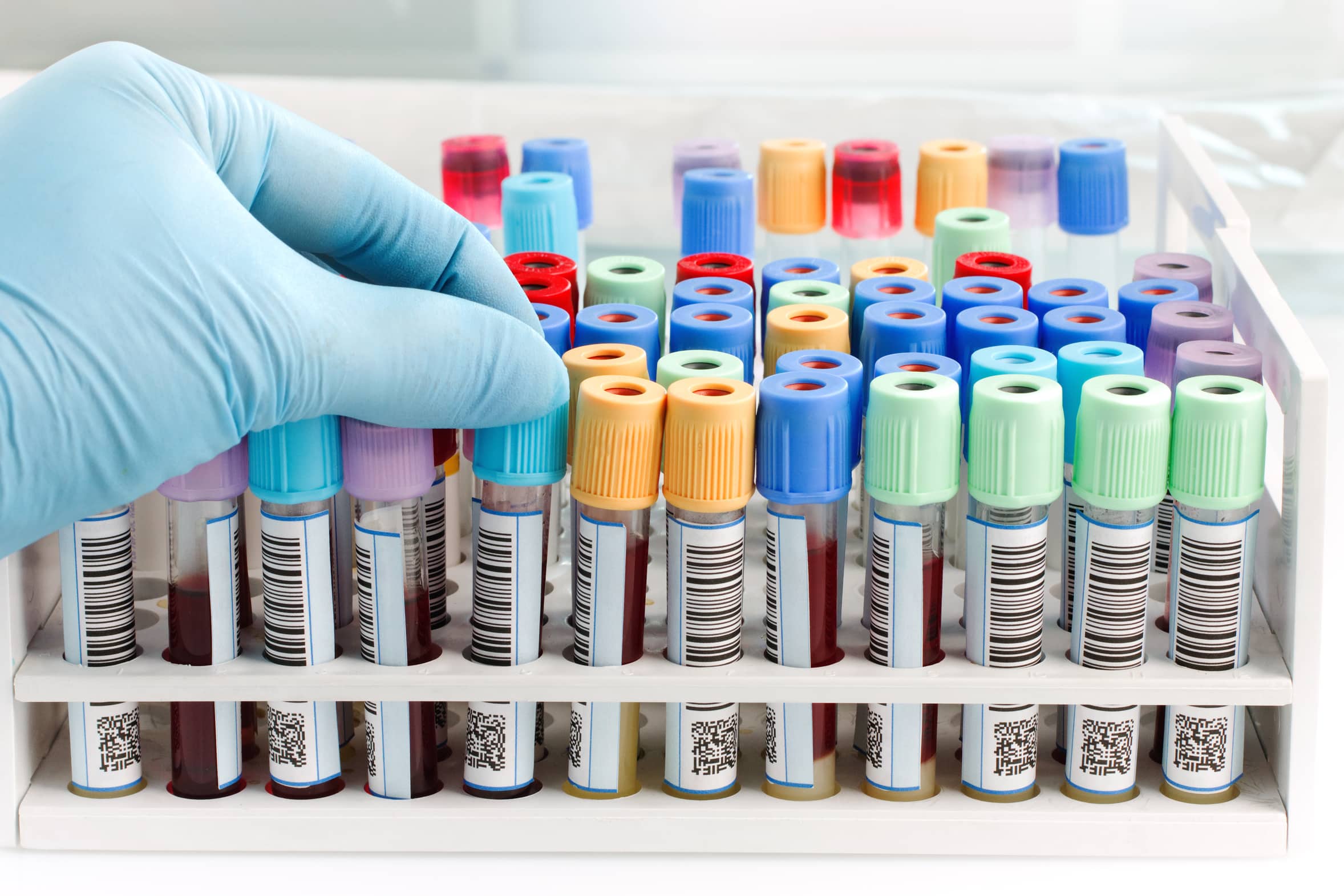
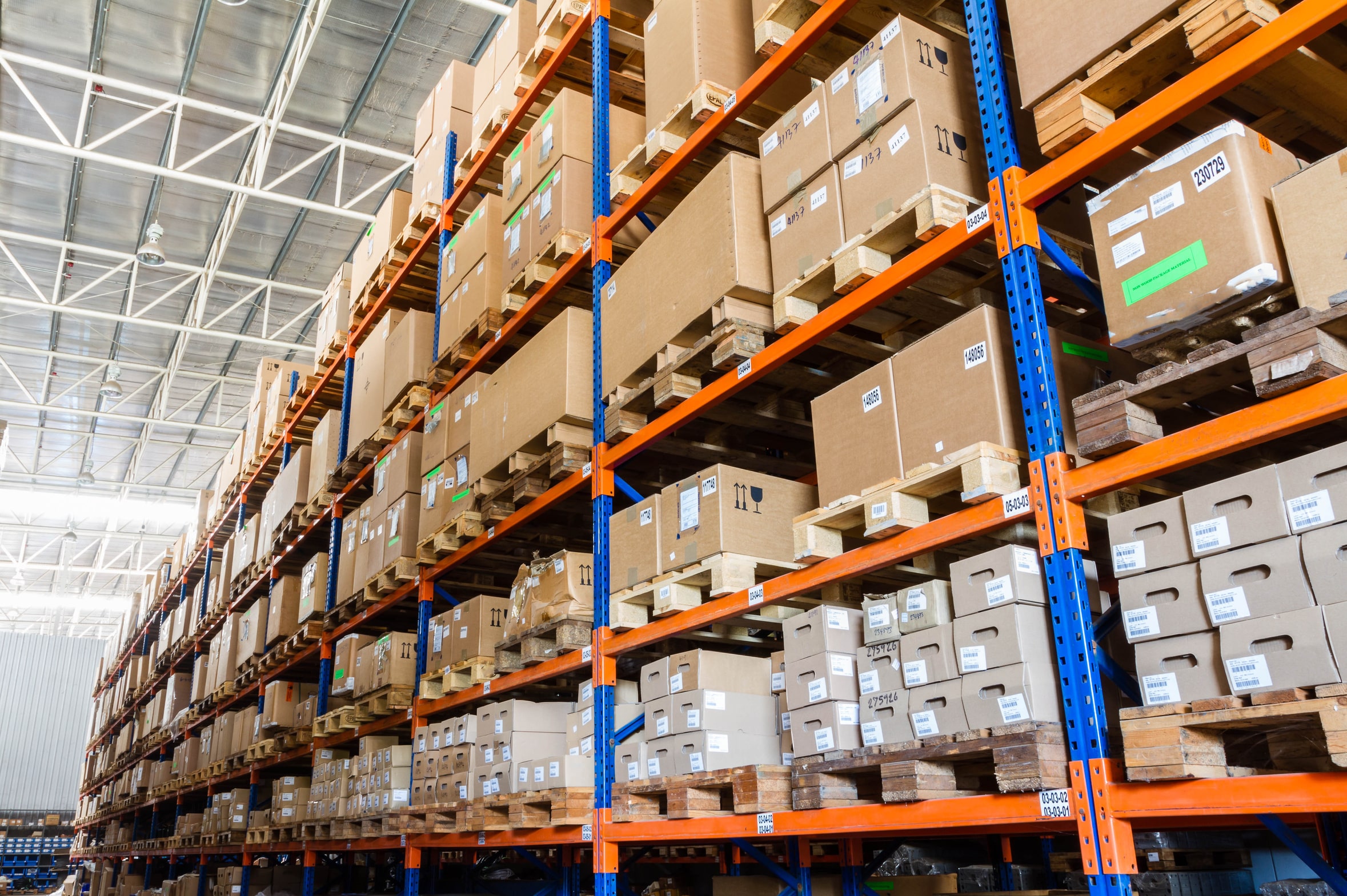
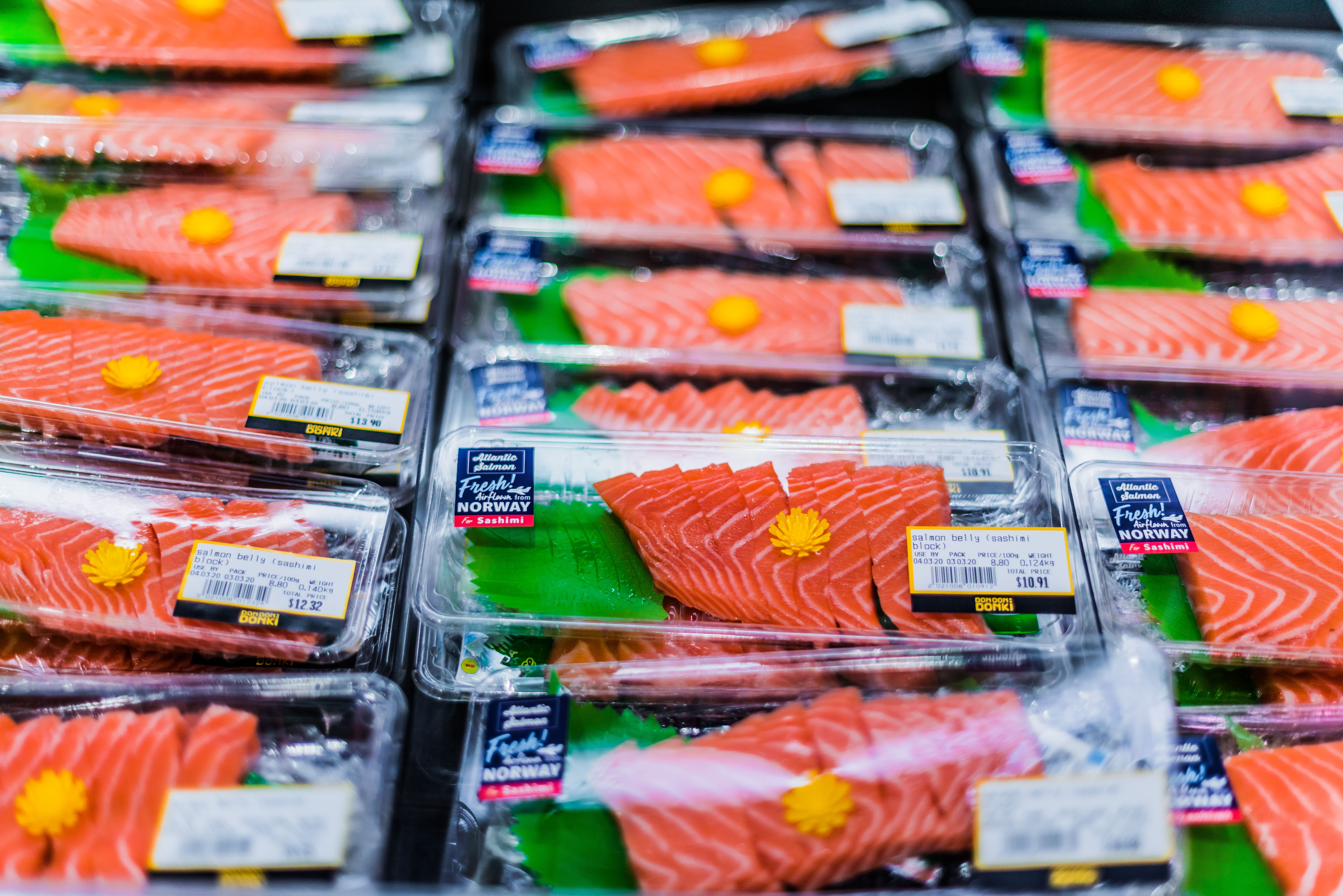
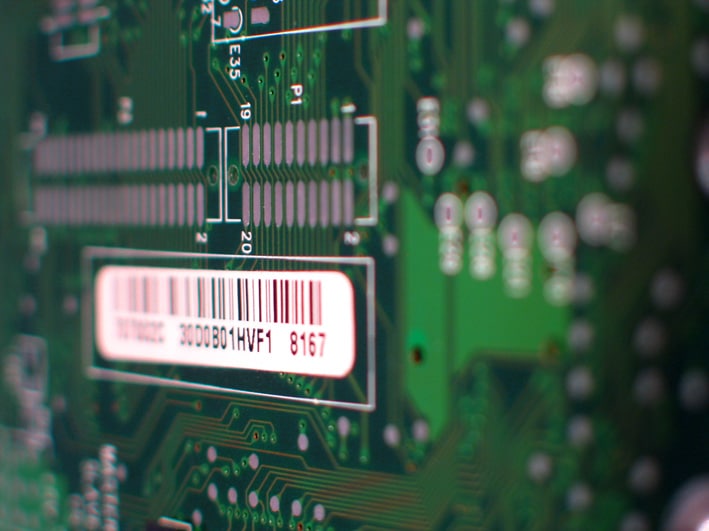
What are the different types of thermal transfer ribbons available on the market?
Now that you have a better understanding of what these ribbons are, it is important not only to know that there are different types but also to get to know each one. As the thermal transfer ribbon product has various applications, different models are recommended depending on the case. Here are the specific features and ways of using each one:
- Wax Ribbon: Wax ribbons are less expensive than other thermal transfer ribbons. They offer excellent performance for printing on paper materials, such as cardboard or coated paper. Their use is recommended for variable information that doesn’t need to last as long, making them ideal for temporary labels or short-term applications.
- Resin Ribbon: Resin ribbons are much more resistant and more expensive than wax ribbons. This makes them suitable for labels that will be subjected to abrasive processes, chemicals, friction, or extreme temperatures. This is why the chemical and food industries, as well as laboratories, prioritize resin ribbons for durable labels.
- Mixed Ribbon: With a mixture of wax and resin, mixed ribbons are used for products that require intermediate resistance. They are perfect for cases in which the printing needs to be more durable, but will not undergo as much wear and tear as in harsher environments.
- Textile Resin Ribbon: Textile resin ribbons have been specially developed to withstand domestic and industrial washing without deteriorating. They also resist the action of detergents and the high temperatures of dryers and irons. The printing is compatible with the most common materials used for clothing labels, ensuring high resistance in textile applications.
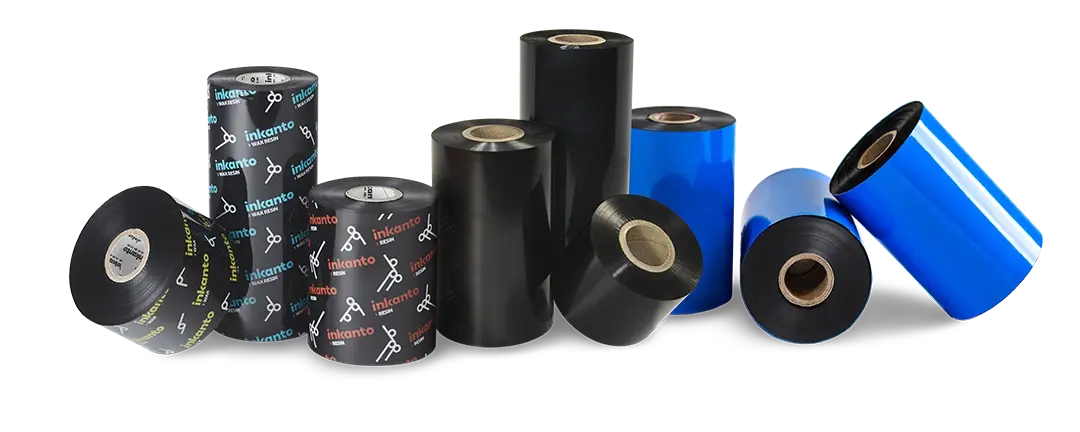
Best practices for choosing and using thermal transfer ribbons
To get the best results from your thermal transfer ribbon, consider the following tips:
- Choose the Right Ribbon for Your Application: Select a wax, resin, or mixed ribbon based on the durability needs of your labels.
- For short-term use: Wax ribbons.
- For abrasive conditions: Resin ribbons.
- For intermediate resistance: Mixed ribbons.
- Consider the Printhead Type: Ensure the ribbon you choose is compatible with your printer. Some printers may require a specific type of ink or ribbon.
- Printer Settings: Adjust the printer settings to ensure optimal performance, especially the heat and speed to avoid print quality issues.
- Store Your Ribbons Properly: Keep them away from direct sunlight, extreme temperatures, and humidity to preserve their quality.
What printers are compatible with thermal transfer ribbons?
Printers compatible with thermal transfer ribbons include direct thermal printers and thermal transfer printers. Specifically, models from brands like TSC, Sato, Intermec, and Citizen are designed to use them. These printers utilize a heated printhead to transfer ink onto the label material, making them suitable for printing high-quality, durable images and text.
Now that you know the science involved in making the different types of thermal transfer ribbons, get in touch for a quote! The experts at ARMOR-IIMAK, a global market leader, will also be able to advise you on the best ribbon for your chosen base material.